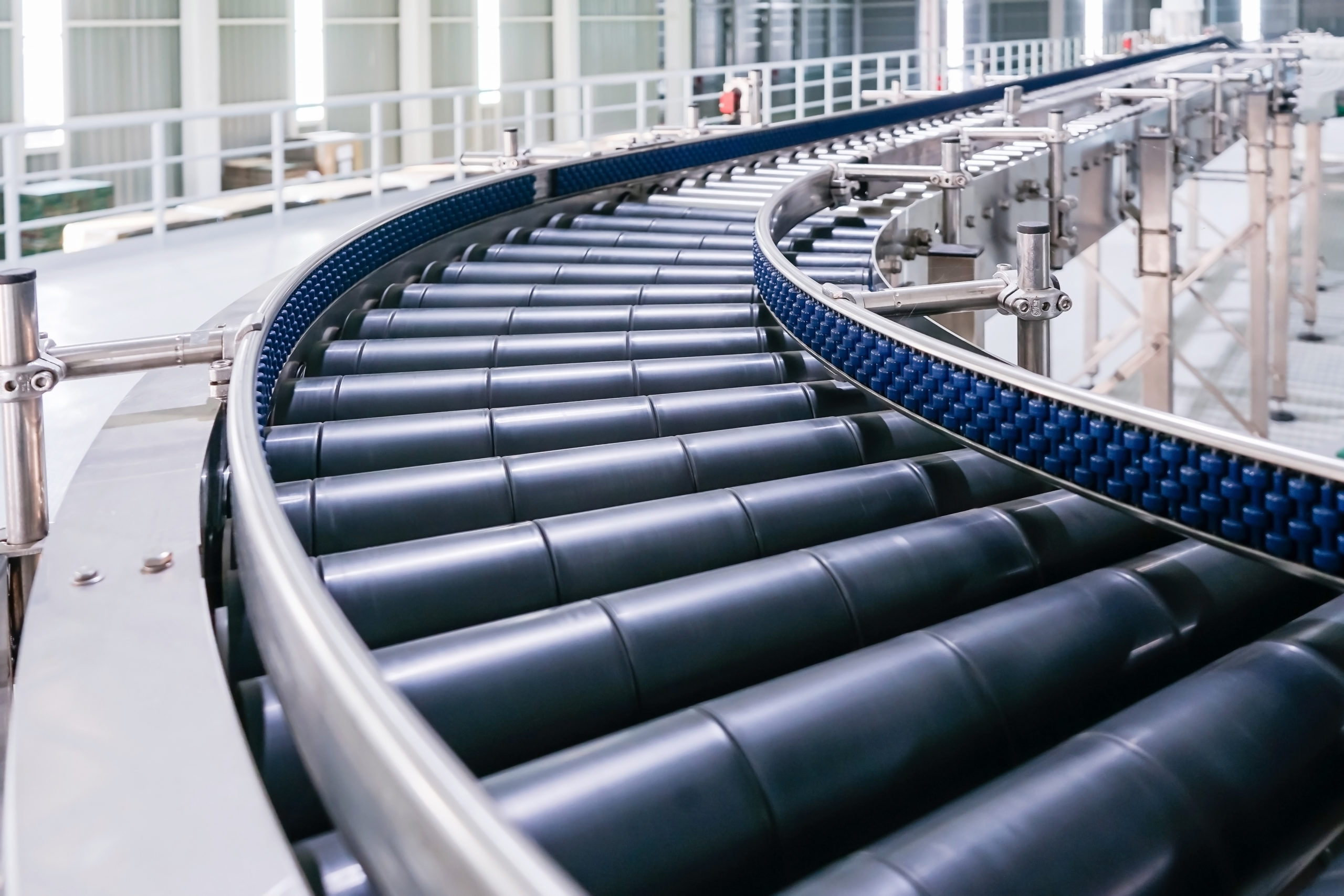
08 Apr Conveyor System and Technology Trends
Conveyor systems have enhanced the way manufacturers move materials at each stage of production for well over a century. Primitive 19the century conveyor belts that moved massive coal and ore loads paved the way for today’s whisper-quiet, super-efficient models. Learn more about why a conveyor system is still essential to today’s manufacturing.
While modern conveyors still transport raw materials and industrial goods, companies today also trust the capabilities of conveyor technology to handle complex automated processes. Often, modern conveyors transport fragile sophisticated components or interact with advanced robotic systems to facilitate manufacturing and distribution processes.
Conveyor system technology will continue to evolve over the next several years, marrying emerging commercial innovations with industrial advances across a wide range of industries.
Conveyor System Trends to Watch
Over the next 3 to 5 years, industry thought leaders expect to see many significant advancements in conveyor systems technology. Conveyor system design professionals are taking notice of these 11 trends as they engineer the conveyors of tomorrow.
1. Quiet Operation
The best conveyors are those that seamlessly integrate into the manufacturing process. Sound is part of that integration. Traditional chain-operated conveyors are being updated with automation that utilizes quiet, energy-efficient powered rollers. Low-voltage, low-torque motors help to decrease vibration and noise as well. Quieter operations can even improve employee communications and work habits on the production floor.
2. Innovative Placements
Factory space comes at a premium. Every square inch of manufacturing floor and shipping operations represents a financial investment. Engineers are developing innovative conveyor systems and conveyor system cable assemblies that work together to function in the open space above factory operations. This innovative use of space can improve manufacturers’ return on their real estate investment.
3. Greater Simplification
There has been an increase in manufacturing demand for complex, highly automated conveyor systems, but smart companies are taking a look at simple applications as well. A straightforward belt or roller conveyor system in the right place can bring measurable improvements to the manufacturing process for little investment. Employees who can perform their jobs with less moving and bending are more efficient and more satisfied.
4. Distributed Control
The Internet of Things (IoT) is transforming the manufacturing process, extending the production “floor” well beyond a factory’s walls. Distributed autonomous controls reduce the need for expensive central processors and tamp down on the expense of hiring large engineering teams.
5. Retrofitted Systems
When producers need new conveyors, they often cringe at the thought of going through the hassle, expense, and downtime involved with upgrading their facilities. Modern conveyor system manufacturers are developing retrofit kits that can convert existing gravity roller conveyors to brand new systems that are motorized, quiet, and efficient.
6. Warehouse and Distribution Growth
Alongside the explosive growth of the e-commerce sector has come an expansion of associated warehousing and distribution. Amazon, for example, expanded its warehousing capacity to a growth rate of 35 percent between 2007 and 2017. Conveyor systems are allowing the Amazons of the world to meet the delivery demands of their customers. This is especially true in the Asia Pacific and North American markets.
7. Flexible Assembly Lines
Assembly lines and their conveyor systems must offer the flexibility required to meet shifting customer demands. Conveyor guidance controls, transfer capabilities, and other accessories are likely to need adjustments when these situations occur. Modular conveyors that can be easily moved from line to line can fulfill this need in only a matter of minutes.
Retractable tail conveyors are one example of innovation in conveyor flexibility. These conveyors allow one end to shorten or lengthen depending on needs. This can help to distribute products across another conveyor, change product orientation, or even improve quality control.
8. Robotic Applications
Robotics will continue to influence manufacturing processes in the coming years. Automated robotic interactions with conveyors are likely to increase. One emerging solution is the advancement in pallet conveyor systems. These systems are ideal for applications that require precise movements and exact positioning of parts. Robotics engineers can program a pallet system to start and stop at specified intervals that sync up with robotics interactions or other processes. Pallet conveyors are becoming more popular in the automotive, medical device, and electronics manufacturing processes.
9. Advanced Conveyor Materials
Designers are increasingly integrating advanced materials into conveyor technology. For example, “detector” conveyors that use food-grade belts can help to keep food manufacturers in compliance with FDA requirements in the U.S. These belts are bacteria-resistant and can detect minuscule parts, making them ideal for this application.
10. RFID Integration
Radio-frequency identification (RFID) technology is showing up across several market segments. The ability to track products and processes in real-time can significantly enhance logistics operations, improve customer service, and improve supply chains from the ordering stage through delivery.
When it comes to conveyors, RFID technology is being integrated into self-contained conveyor systems that automatically make control decisions and allow for multiple processes across multiple products to run simultaneously.
11. Eco-Friendly Conveyors
Manufacturers are embracing the trend to make ecological improvements to their operations to comply with industry regulations. Consumer buying preference is trending toward environmentally-friendly products as well, influencing manufacturer decisions about internal processes. Eco-friendly conveyors are designed from the ground up to be more energy-efficient while maintaining similar efficiency to standard conveyors. Engineers often achieve this balance through a narrower belt design.
Other eco-friendly advances include energy-efficient motors, automatic sleep controls, regenerative motors, variable speed drives, and motor-driven rollers that consume less energy.
Helping Manufacturers Select a Conveyor System
Production facility operations teams working through decisions about their conveyor needs can benefit from learning more about these emerging trends. Today’s conveyor offerings represent a dizzying array of options and impressive functionality, but not all conveyors are appropriate for all productions. operations.
The good news is that conveyor manufacturers can build systems to the specifications of a given manufacturer. There is sure to be an ideal system that improves the efficiency and output of any given production line.
The first step is to take a high-level look at what end goals a manufacturer hopes to achieve. Staying focused on what problem each conveyor can solve is a surefire way to arrive at the ideal conveyor design.
NAI works with industrial equipment companies who manufacturer conveying and other material handling systems to help them solve their interconnection needs to power, control and operate their equipment efficiently and reliably. Expert engineers design the appropriate interconnect solutions to maximize value and quality.