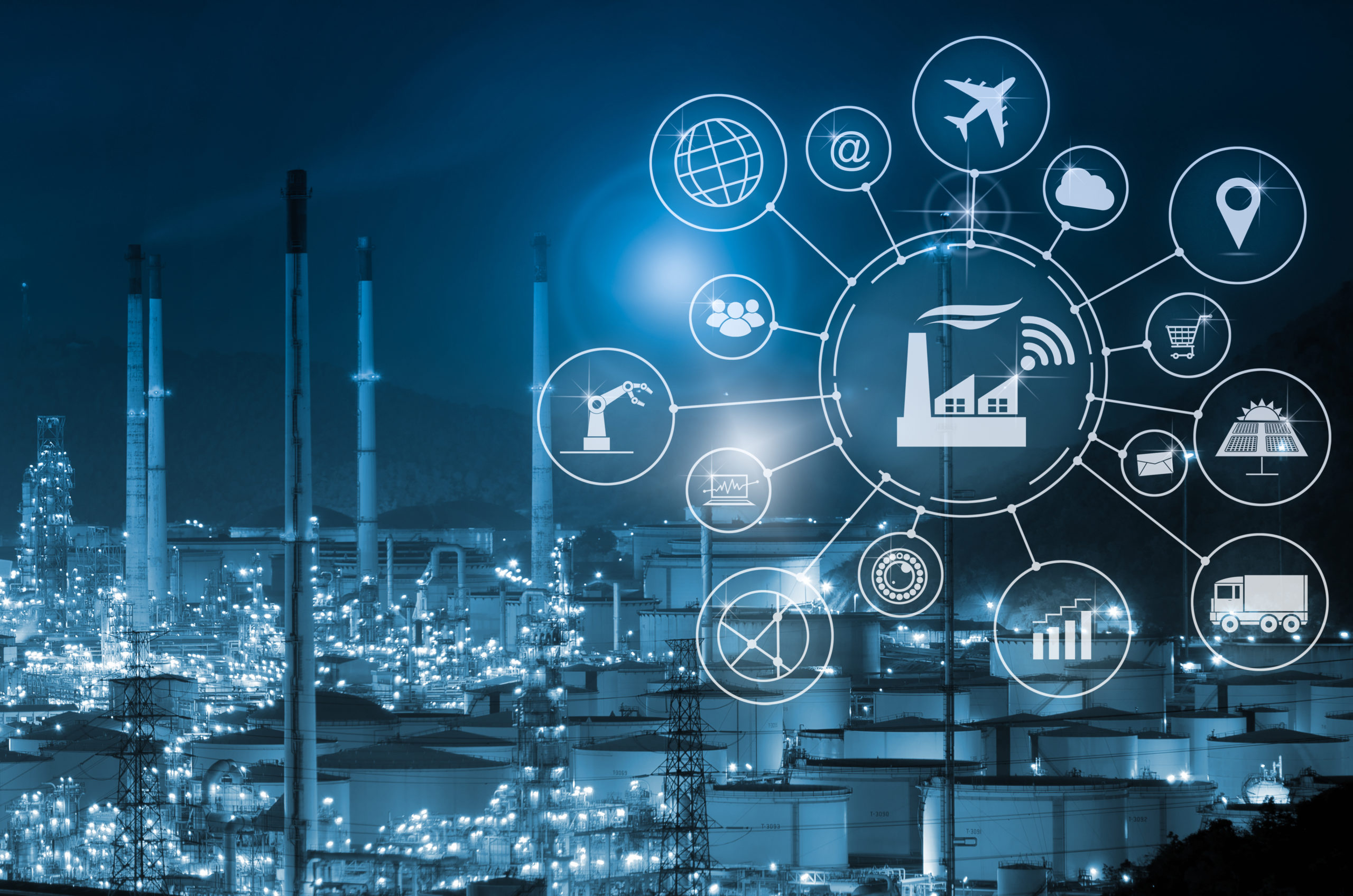
19 Nov Trends that NAI Group is following In Industrial Networks and Technology
The last few years witnessed the rise of new technological advancements and innovations that radically changed the production and manufacturing industries. Additionally, there has been a change in the community and social attitudes towards manufacturing as a whole. The demand for greener and more ethically produced goods coincided with an increase in demand in general. NAI has closely followed previous industry trends and continues to follow upcoming trends.
Now, as large-scale manufacturers and producers recover from the effects of COVID-19, most are committed to improving their industrial practices. This collective effort shared among manufacturers of varying sizes and industries spawned the rise of multiple trends in industrial technology. Keep reading to learn the trends that NAI Group is following.
Workers’ Safety and Security
Employee safety became a priority in early 2020, and it still stands strong as one of the most prominent industry trends. While it started as essential and often government-enforced measures of social distancing and sterilization, it gradually bled into other areas of the workplace.
Businesses worldwide are addressing their employees’ safety concerns more urgently than ever. This includes increasing worker accessibility to profession-appropriate protection gear and providing extensive training before working with heavy machinery. Many employers began praising this new approach. It increased employee trust in their employers and reduced their anxieties around workspace injury, allowing them to be more productive and efficient.
IoT Is Getting Bigger
IoT isn’t a new arrival in the manufacturing industry, but it’s been solidifying its presence over the past few years. In fact, according to a recent survey, a third (31%) of all manufacturing processes rely on smart applications and gadgets.
This upwards trend coincides with an increase in the accessibility of digital devices and gadgets. Not only are devices more affordable and specialized than ever, but as a manufacturing manager, IoT applications can reduce the load by automating various procedures and keeping all parts of the industrial complex in the loop.
Virtual and Augmented Reality
The need for technicians to do their work remotely has been present since the turn of the century. However, the recent pandemic turned it into a necessity rather than a plus.
Fortunately, Virtual Reality (VR) and Augmented Reality (AR) were already established innovations when the world needed them most. VR and AR allowed employees to control their equipment and machinery remotely without losing sight of what they were doing.
These technologies also filled a gap in product marketing that the pandemic only made worse. Clients and customers are often reluctant to purchase a product they’ve yet to test or see. Now, however, you can easily render your products and services as either VR or AR interactive videos that give potential buyers a closer look without having to travel to your manufacturing facility.
Manufacturing Equipment Is More Durable
Manufacturers are realizing the importance of sustainability and durability when it comes to equipment. While manufacturing managers were once concerned about finding the right balance between performance, longevity, and price, the scales have mostly shifted towards durability.
Everything from industrial cables and in-factory transportation to digital and electronic devices is becoming more durable. It’s a grand upfront investment, but the cost of repairs over the long run offset the need to replace an entire factory’s worth of equipment every few years.
Industrial Networks Over Traditional Networks
Traditional computer networks are much easier to manage, not to mention they work on a decently large scale. However, it’s only a matter of time before your facility outgrows the capabilities of a traditional computer and data network, forcing you to uproot the current network and replace it with an industrial network.
Industrial networks can transfer data and connect multiple devices on a large scale, allowing them to communicate across massive areas such as buildings, warehouses, and facilities.
Preventative Maintenance Over Reactive Maintenance
Maintenance is an inevitable reality in most industries, especially the manufacturing industry. However, not all maintenance approaches are created equal, nor do they offer the same results. The last few years witnessed a drastic shift from reactive — or emergency — maintenance to preventive maintenance.
Preventative maintenance is the practice of performing routine maintenance of equipment and tracking the health and condition of your assets. In addition to valuable data for analysis, this module minimizes the chances of a complete and unpredictable breakdown of any of your machinery. Such could leave you to deal with costly downtime and emergency maintenance or equipment replacement fees.
Reliance on Big Data for Major Decisions
With the use of tracking software, IoT, and smart tech in general, manufacturing managers found themselves with massive amounts of data unique to their facility. Instead of ignoring it, many started to feed said data into complex analysis algorithms and use the resulting insights to guide their business decisions.
Reshoring and Sourcing Locally
Reshoring and locally sourcing materials is a manufacturing practice that has been gaining momentum since the early 2010s, and it reached its peak in 2020 due to COVID-19’s mass travel restrictions. Sourcing both materials and workers locally doesn’t just allow for better quality control of your products, it also increases your credibility and trust among your client base. Additionally, sourcing raw materials locally allows for faster and cheaper shipping trips that are at a much lower risk of natural disasters and lost revenue.
Investing in Online Tech Training
As the industrial sector becomes more reliant on technology, the need for qualified and experienced workers increases. Instead of letting your current staff go and hiring a new force that’s more skilled with limited company experience, you should aim to train your current staff.
Luckily, tech training — whether it’s using complex software or learning a programming language — can be done remotely and efficiently. This trend is proving to be high on the list of priorities as advanced equipment and gadgets have little to no value without workers that know how to use them.
Industrial Technology Trends & How NAI Can Help
The Industrial sector is only going to grow in size and increase its reliance on technology. However, following beneficial trends can still be costly, especially if it’s not done properly. Having the right components and guidance is essential to successful growth. NAI Group provides large-scale manufacturers fully tested and regulation-compliant interconnect solutions to be integrated into your technological breakthroughs.