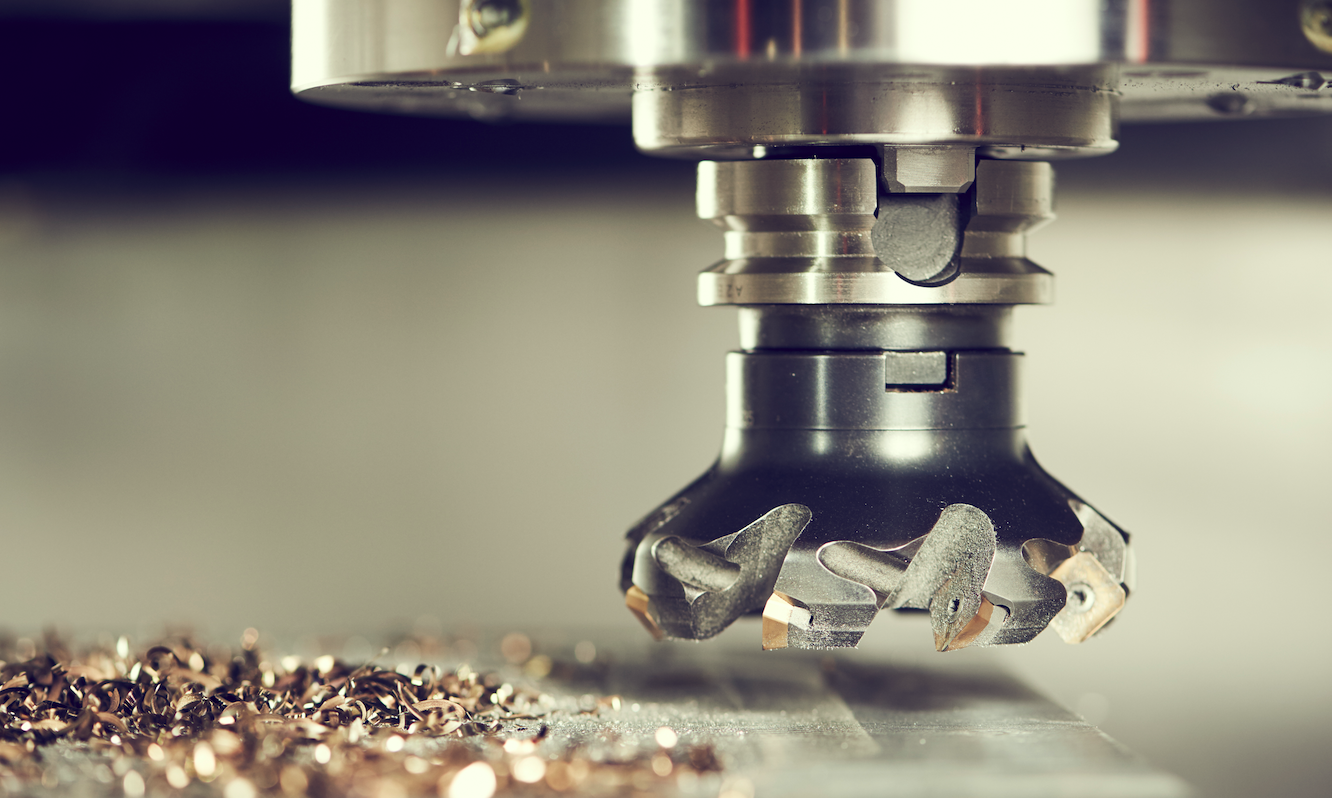
01 Sep Emerging Trends in the Machine Tool Industry
Machine tools are more important than most of us know. They enable the economical manufacture of standardized parts for use in everything from automobiles to aircraft.
Advancements in machine tool technology and innovation-driven by high demand are pushing the machine tool industry forward at a rapid pace. According to MarketsandMarkets, the global machine tool industry is expected to grow from a market size of $77 billion in 2019 to $98.3 billion by 2027.
That projection had to be revised due to the pandemic’s impact on manufacturing plants, which could not conduct business as normal. Even so, the most recent Market Report puts the industry’s growth at $87.4 billion by 2027.
The Future of Machine Tools
Advancements in hardware and software are changing the machine tool industry. Industry trends in the coming years are likely to focus on these advancements, especially as they pertain to automation.
The machine tool industry is expected to see advancements in:
- Inclusion of smart features and networks
- Automated and IoT-ready machines
- Artificial intelligence (AI)
- CNC software advancements
Inclusion of Smart Features and Networks
Advancements in networking technology have made it easier than ever to connect smart devices and build local networks for the machine tool industry.
For example, many devices and industrial edge computing networks are expected to use using single-pair Ethernet (SPE) cables in the coming years. The technology has been around for years, but companies are beginning to see the advantage it provides in building smart networks.
Able to transfer power and data simultaneously, SPE is well suited to connecting smart sensors and networked devices to the more powerful computers driving industrial networks. Half the size of conventional Ethernet cable, it can fit in more places, be used to add more connections in the same space, and be retrofitted to existing cable networks. This makes SPE a logical choice for building smart networks in factory and warehouse environments that may not be suitable for current generation WiFi.
Low-power wide-area networks (LPWAN) allow data to be transmitted wirelessly to connected devices over a greater range than previous technologies. Newer iterations of LPWAN transmitters can go a full year without replacement and transmit data up to 3 km.
Even WiFi is becoming more capable. New standards for WiFi currently in development by the IEEE will use 2.4 GHz and 5.0 GHz wireless frequencies, boosting strength and reach beyond what current networks are capable of.
The increased reach and versatility provided by new wired and wireless technology make automation possible on a grander scale than before. By combining advanced networking technologies, automation and smart networks will become more common across the board in the near future, from aerospace manufacturing to agriculture.
Automated and IoT Ready Machines
As the machine tool industry continues to adopt more digital technologies, we’ll see the manufacture of more machines built for automation and the industrial internet of things (IIoT). In much the same way we have seen an increase in connected devices — from smartphones to smart thermostats — the manufacturing world will embrace connected technology.
Smart machine tools and robotics will likely handle a greater percentage of the work in industrial settings as technology advances. Especially in those situations where the work is too dangerous for human beings to perform, automated machine tools will become more widely used.
As more internet-connected devices populate the factory floor, cybersecurity will become an increased concern. Industrial hacking has resulted in several worrying breaches of automated systems over the years, some of which could have resulted in the loss of life. As IIoT systems become more integrated, cybersecurity will only increase in importance.
AI’s Impact on the Machine Tool Industry
Especially in large-scale industrial settings, the use of AI to program machines will increase. As the machine tool industry becomes automated to a greater degree, programs will need to be written and executed in real-time to manage those machines. That’s where AI comes in.
In the context of machine tools, AI can be used to monitor the programs the machine is using to cut parts, making sure they don’t deviate from the specifications. If something goes wrong, AI could shut the machine off and run diagnostics, minimizing damage.
AI can also assist in machine tool maintenance to minimize and address problems before they happen. For example, a program was recently written that can detect wear and tear in ball screw drives, something that had to be done manually before. AI programs like this can help keep a machine shop running more efficiently, keeping production smooth and uninterrupted.
CNC Software Advancements in the Machine Tool Industry
Advancements in computer-aided manufacturing (CAM) software used in CNC machining allows for even further precision in manufacturing. CAM software now allows machinists to use digital twinning — the process of simulating a physical object or process in the digital world.
Before a part is physically manufactured, digital simulations of the manufacturing process can be run. Different toolsets and methods can be tested to see what is likely to produce the optimal result. That reduces cost by saving material and man-hours that might have otherwise been used to refine the manufacturing process.
Newer versions of machining software like CAD and CAM are also being used to train new workers, showing them 3D models of the parts they’re making and the machine they’re working with to illustrate concepts. This software also facilitates faster processing speeds, meaning less lag time and quicker feedback for machine operators while they work.
Multi-axis machine tools are more efficient, but they also come at a higher risk for collision as multiple parts work at once. Advanced software cuts down on this risk, in turn cutting downtime and lost materials.
Machines Working Smarter
The machine tool industry of the future will produce machines that are smarter, more easily networked, and less prone to error. As time goes on, automation will become easier and more efficient through the use of machine tools guided by AI and advanced software.
Operators will be able to control their machines via computer interface more easily and make parts with fewer errors. Networking advancements will make smart factories and warehouses easier to achieve.
For more information on how NAI can help machinists meet the challenges of the machine tool industry trends with custom interconnected solutions, contact NAI today to Ask An Expert.