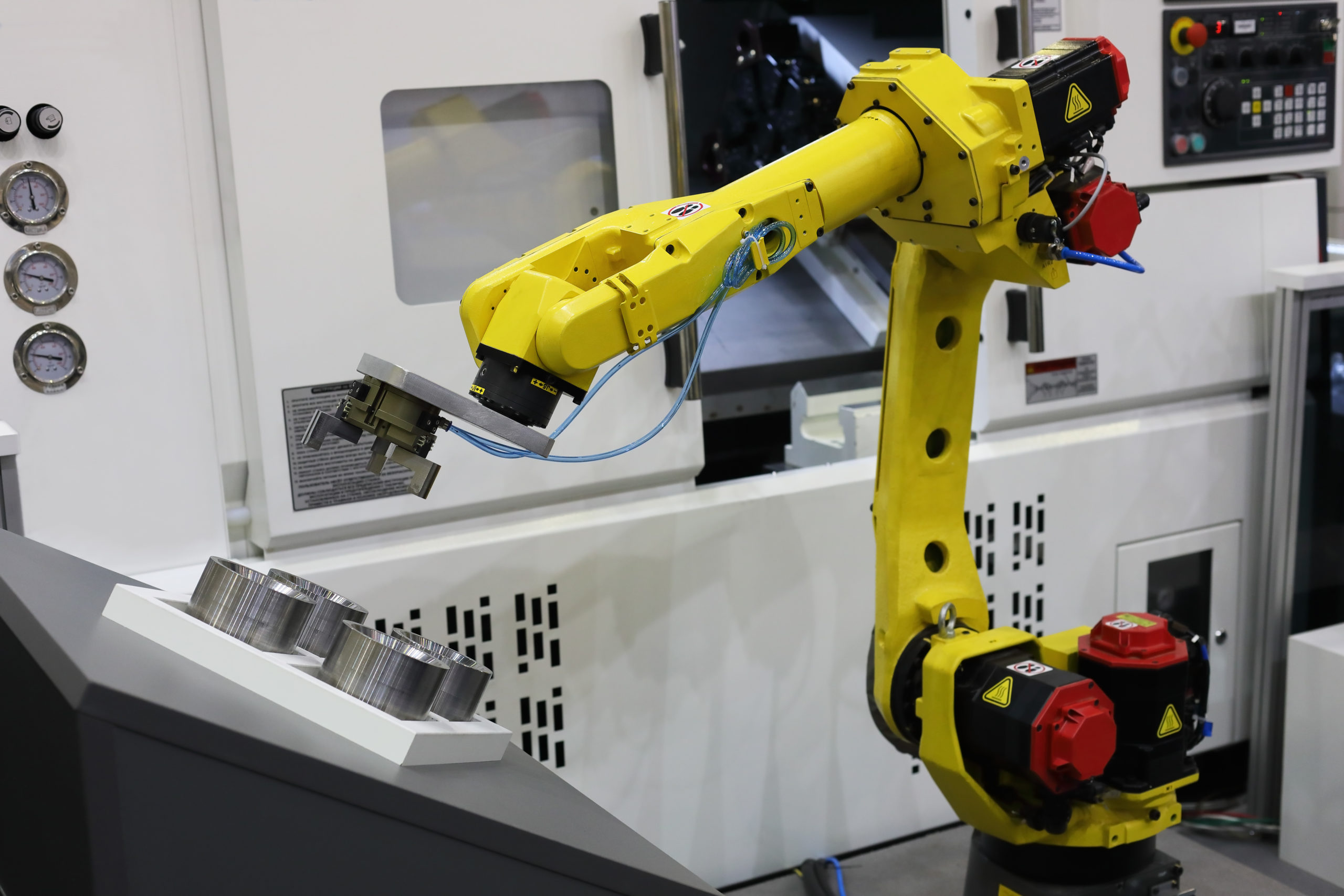
25 Nov Cobots and Their Place in Today’s Workforce
Robots play important roles in today’s workforce, designed to tackle the “4 D’s of robotization:” jobs considered dull, dirty, dangerous, and dear or expensive.
However, because of the risk of physical harm, companies usually need to keep robots separate from employees or limit their functionality. While a standard of worker safety, this reduces robots’ potential and applicability.
Businesses looking to advance workplace output and efficiency must balance this risk without endangering employee welfare.
Cobots — or collaborative robots — fill this gap. These machines are designed to safely work hand-in-hand with workers, enhancing the work of their human counterparts. Cobots in manufacturing handle rudimentary tasks so that your employees can focus more on aspects that require higher abilities, like problem-solving or creative strategy.
Defining Cobots
Cobots are intentionally built to interact with people. They aren’t designed to replace workers but rather enhance the efficacy of many tasks. Fully automating the manufacturing industry isn’t the goal, as companies need the human touch to field flexibility and on-the-fly adjustments.
Think of a cobot like a wheel. The wheel speeds up a person’s ability to get from one place to another with less effort — but without human interaction, a wheel doesn’t serve much function.
The International Federation of Robotics defines a cobot as meeting one of four criteria:
- Co-existence: Working alongside a human worker with no direct overlap
- Sequential collaboration: Performing a task before or after a human worker
- Responsive collaboration: Responding directly to a human action
- Co-operation: Working with humans toward the same task
What are the Benefits of Cobots?
In these roles, cobots are a form of augmented intelligence. Instead of replacing workers with automated machines, cobots boost human capabilities with improved strength, precision, and logistical power.
Compared to a traditional robot, a cobot is cheaper and easier to program — and re-program — giving it greater flexibility to perform a wider variety of tasks, even across departments.
This quick and adaptable installation also means cobots can:
- Work after hours or overnight
- Be moved around the floor to serve different functions
- Supplement a shortage of skilled workers
- Improve production quality
- Boost employee satisfaction by taking on mundane or dangerous tasks
These effects work to best leverage a company’s skills and resources to boost output, efficiency, and overall profit margins.
What Do Cobots Do?
Some cobots use common programming languages that are easy for programmers to install. Newer versions use no programming at all, however.
These cobots learn from their human operators, using enhanced agility and speed to perform various tasks like:
- Manual pick and place, one of the most repetitive tasks performed by human workers
- Machine tending, like tool changes or refresh of raw materials
- Process-oriented jobs like dispensing, welding, or assembly
- Focused precision tasks like continuous wire or cable installation
- Packaging and palletizing products before leaving the factory floor
- Finishing tasks and quality inspection
Depending on the cobot, they may also be capable of lifting, transferring, and organizing things independently. They can come with specialty functions as well, like cobots for cable and wire assembly. This range of capabilities can minimize the need for other costly equipment and streamline tasks prone to human error, like packaging and quality control.
Here are some specific ways companies use cobots today:
- Ford uses cobots to help workers fit shock absorbers to cars, relieving the job’s physical intensity
- Dynamic Group, operating out of Minnesota, employs cobots to precisely inject molded parts for medical and electronic products, quadrupling production
- BMW employees work in tandem with cobots to make the riveting process more efficient
- India-based manufacturer CATI used cobots to reduce customer rejections from faulty products by 15-20%
How Will Cobots Change Manufacturing?
Many industries are quickly adopting cobots, including the manufacturing realm. By 2026, their use is expected to grow by almost 42%.
Because cobots can adapt to changing requirements, they increase productivity and cost-savings for small and large businesses alike — all while improving employee safety and satisfaction.
On the Floor
Cobots’ role in manufacturing is expected to broaden even further, especially in product assembly. Today’s demand for new products — and shortening product life cycles — pressures companies to reduce time-to-market and find ways to improve supply chains that can withstand the pace of demand.
This idea of “lean automation” relies on finding the right balance of automation while keeping the human touch at the center of processes. Excessive automation doesn’t work — as Tesla learned in 2018 when it was forced to roll back its complex network of robots in one factory, slowing production and disappointing investors.
Experts predict this balance exists where cobots will handle the hum-drum manufacturing aspects, while human workers ensure strategic planning, material flow, and parts of product inspection.
In the Workplace
Cobots can enable huge productivity increases. According to one MIT study, collaborative human-cobot teams have 85% less idle time during the workday. But cobots don’t replace human activity — they modify it. Cobots take on the dull, mundane, and repetitive tasks, allowing human workers to tend to cognitive, strategic, and creative roles.
Studies support that these more challenging roles — and the training, advancement, and opportunities that emerge — lead to higher job satisfaction. Happy employees are a company’s best asset, directly linked to organizational performance, along with improved worker productivity, quality, and retention.
A common automation myth is that cobots will destroy jobs, but this is an unfounded claim. One case study reports that using cobots led to ten times the production yield and a 16% increase in staff. Adopting new technologies also attracts younger workers to manufacturing, creating more jobs and sustaining the industry’s growth and development.
Leveling the Playing Field
The first industrial robot joined General Motor’s assembly line in the 1960s. The 4,000-pound arm — which served a single job — came with a $25,000 price tag, more than $215,000 today after adjusting for inflation.
But automation’s competitive edge isn’t just for the GMs of the world anymore. Compared to these early models, today’s cobots are cheaper and smaller, making them much more accessible to a range of businesses. Since they’re easy to install and program, cobots don’t require a dedicated IT department to operate. Teams can also re-program them as needed — extending their range of functionality and value for money.
These benefits help smaller companies to compete with global giants. Case studies show that cobots allow small manufacturing businesses to overcome disadvantages like market proximity, labor access, and quickly changing trends.
This improved competition leads to better innovation and producer accountability, meaning higher-quality products and services for manufacturing consumers across the board.