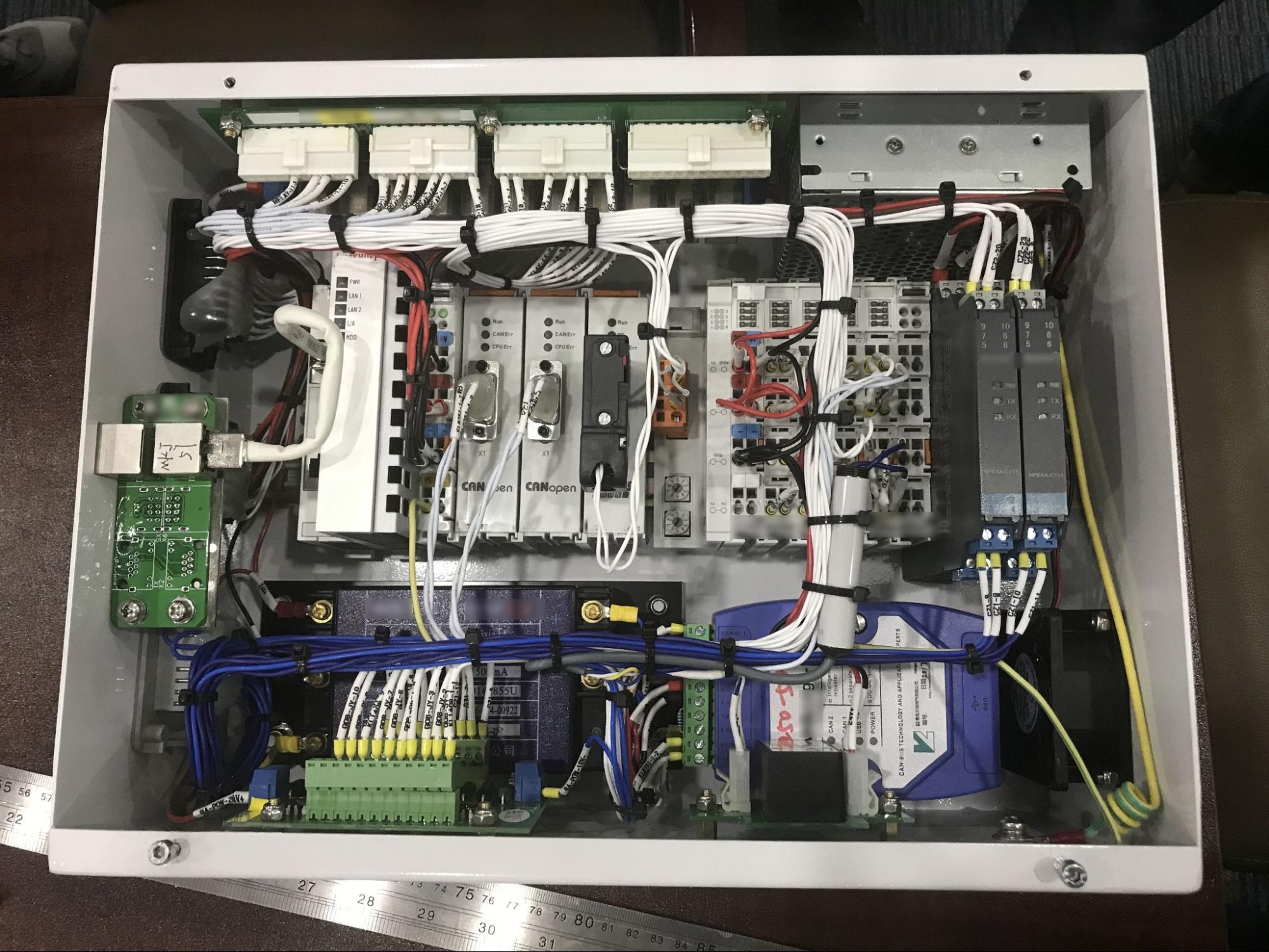
08 Aug Future Trends in the Box Build Industry for 2022
As our society continues to become more and more technology dependent, we continue to see its rapid evolution. Many manufacturing capabilities that brought us to this point aren’t going anywhere anytime soon, but are changing to meet the new demands. One of these important manufacturing capabilities is in the area of Box Build Assemblies. Here are some of the Future Trends in the Box Build Industry for 2022.
But before we dive into the future of box builds, first you need to have a clear understanding of what a box build assembly is. Who better to explain what a box build assembly is than the best box build assembly manufacturers? NAI is a global leader in providing the best quality box build assemblies available. Here’s what you need to know about box builds.
What Are Box Build Assemblies?
No cardboard here, box build assemblies are an essential part of most electronic controls, devices, and automated machinery. Without them, the world of product manufacturing, security, networking, and other industries wouldn’t look the same.
A typical box build is a combination of electronic components that can include printed circuit boards (PCBs), logic processors, hybrid cables, and other electronic components housed in an enclosure.
What are Printed Circuit Boards?
Printed circuit boards are one of the critical components involved in most box build assemblies. These electronic devices are found in almost every electronic device you use daily. Essentially, a PCB is an electronic circuit that is used in the previously mentioned devices to give a pathway to the electronic components while also providing logic, mechanical support, instructions, and more.
These critical devices are made through various combinations of unique sheets of non-conductive materials. Plastic and fiberglass are common examples of materials that easily contain copper circuitry.
What are Logic Processors?
Another common component contained by box builds are logic processors. What are logic processors? Logic processors are components that are basically a simple measure of how many cores an operating system can see and address.
In simple terms, a core is essentially the processor that does the handling of information in electronic devices. The more cores, the more processes the device can do. You can measure this by the number of cores and threads available.
To do this you find the product (multiplication) of the physical number of cores with the number of threads each individual core can handle. For example, an 8-core 8-thread CPU would mean the number of logical processors you have would be 8.
What are Hybrid Cable Assemblies?
Hybrid cable assemblies are something NAI is an expert in manufacturing. What are hybrid cable assemblies? Well, hybrid cables are just a custom type of cable that has different sizes and types of conductors or other components that are incorporated into one, simple and organized unit, such as copper conductors combined with fiber optic cables.
These custom hybrid cable assemblies can provide a wider range of functionality than other cable assemblies. Hybrid cable assemblies meet the performance requirements of complex devices without the typical clutter associated with these complex cable assemblies.
Hybrid cable assemblies are ideal for use in industries such as medical, industrial technologies, and telecom. With custom hybrid cable assemblies, NAI helps power, control, or operate each of these critical industries. Our team creates custom hybrid cable assemblies to meet our partner’s exact specifications.
How Do Box Build Assemblies Work?
When it comes to a box build assembly, they can be virtually any size or complexity level! A box build could be a small component of a consumer device, the electronic controls of an appliance, part of a building’s HVAC system, part of a control system for a mining operation, or a large component of a utility-scale control system.
Box builds are, essentially, a self-contained electromechanical assembly that completes modular processing and logic tasks. These components can be manufactured separately from the final product or system, and are purchased by NAI’s global sourcing team for the best value to the customer. The boxes themselves can be molded plastic or metal, the material determined based on the conditions of the operation and location. NAI also has in-house molding capabilities for certain enclosures.
In some cases, a box build may contain all the electronic components of a product, such as an all-in-one control module and user interface of a piece of industrial machinery. Alternatively, a box build assembly may be part of a larger system and perform just a few specific functions, such as a component of an appliance that controls timing cycles.
By using prefabricated and pre-terminated box builds, final products can be assembled more easily, upgrades can be completed faster, and electronic components become simpler to troubleshoot and replace in the field. In addition, enclosures for these components can be specially designed to protect their components. For example, they can be designed to protect their contents from heat, water, physical damage, or magnetic interference.
These box-build assemblies are critical for industries that need reliability, like life-saving machines in the medical industry or necessary communication infrastructure towers in telecom to provide 5G and other services.
Box Build Assemblies Characteristics:
- Contain electronic and electromechanical functions in larger installations
- Can be installed or replaced as discrete components
- Include enclosures that protect electronic components used in their application environment
What is the Future of Box Builds?
The path ahead of electromechanical design is unpredictable, to say the least. But NAI is keeping a keen eye on the future. The ways that box builds evolve in the future will be dependent on changes to the component technology, as well as changes to their installation environments. Here are a few developments in the box build industry that NAI will be paying attention to in the coming years.
Box Builds and Flexible PCBs
The capability of box builds is somewhat dependent on printed circuit board technology that we discussed previously. These technologies are evolving to become more efficient and meet new requirements. Flexible circuit boards are quickly becoming a standard option for PCB designers and they offer some interesting features for box build design.
Other than the obvious advantage of being able to be folded or curved into smaller spaces, flexible circuit boards are resistant to high heat and less susceptible to mechanical damage, which can ease some demand on the enclosure. The final box build assembly can therefore be cheaper, lighter, and smaller than those utilizing traditional PCBs.
These advances will help nearly every industry as components and devices continue to become smaller to meet physical space demands.
3D-Printed Circuit Boards for Use in Box Build Assemblies
3D printing technology now allows for circuit boards to be built in tiny layers, each with circuits as complex as a traditional PCB. As each layer has unlimited potential to be connected to other layers, 3D-printed PCBs make use of dense space like never before.
Box builds utilizing this technology will eventually become smaller, more customized, and more modular than ever. 3D-printed circuit boards will allow infinite options for customized mounting, connection ports, and circuits fitting in the smallest and most oddly shaped spaces.
Changes in the Operating Environment of Box Builds
The environment in which a box build is installed and operates has as much bearing on design considerations as the technology inside. Box builds continue to find their application in new places. They don’t just sit on desks, on a machine or in padded cases anymore — they’re in tractors, jackhammers, cars, spaceships, and beyond.
Many electrical components are used in conjunction with green energy sources, and therefore are subject to the elements to which the energy source is also exposed. Everything from typical outdoor conditions, high winds, salt water, UV rays, and intense pressure can affect the components.
This means that box builds must be designed to resist every respective condition to which it is subjected in its application. Heat, cold, vibration, water infiltration, corrosive environments, and mechanical stress will heap requirements onto box builds. NAI is continually investigating new materials and design approaches to meet the increasingly complex demands of box build assemblies.
Changes in the Larger Environment of Electronic Components
A box build’s environment isn’t the only determinant of the physical characteristics needed to operate effectively in its installed location. Box builds must also meet the requirements of the market and a sustainable product lifecycle.
As outdated electronic equipment continues to flood landfills, designers have started taking a longer view of the lifecycle of electronics. Efforts such as considering recyclability during the design stage are reshaping the landscape of electronic component design. Biodegradable PCBs are even in development. NAI continues to develop box builds to meet our customers’ quality, economy, and sustainability goals.
Find the Best Box Build Assembly Manufacturer
No one knows precisely what the future of the box build assembly industry will bring. But at NAI, we have our eye on the newest trends in this space to meet our goal of advancing our clients’ technologies and operations for their products.
Our global team of engineers and researchers continues to analyze emerging trends, technologies, and new manufacturing materials to improve the box build assemblies we produce. We constantly seek ways to create the most cutting-edge box build assembly technology.
At NAI, it’s not just our expertise in engineering high-performance hybrid cable assemblies and box builds, but it’s also our global manufacturing facilities that are a unique advantage. Our manufacturing plants in Gaylord MI, Hermosillo, Mexico, and Suzhou, China provide a global footprint we leverage to overcome supply chain disruptions, reduce lead times, and deliver the quality cable, harness and box build assemblies our clients need.
We leverage our global pool of talent and manufacturing capabilities to meet our specific partner requirements for their box build assemblies. See some of our box build manufacturing capabilities.
Learn more about how having NAI as a partner can bring not only fresh insights and cutting-edge designs, but also scalability and a high level of quality assurance.