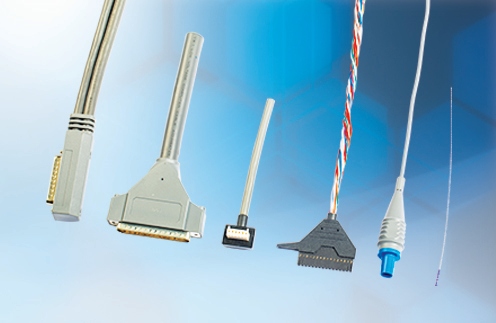
23 Feb Plastic Molding Capabilities for Manufacturing Cable Assemblies
Manufacturing an electromechanical assembly, a cable assembly, or wire harness requires careful attention to many design considerations. Plastic molding is a cost-effective, efficient process that protects the connection for durable and safe use.
Despite the rise in wireless technology, our digital world depends on cable assemblies. Circuits, cables, cords, and conduits make up essential components of nearly every electromechanical assembly, cable assembly, and harness. While they’re used primarily in the electronics sector, they rely on a manufacturing method that’s been around for a long time: injection molding.
Invented in 1742 and popularized in World War II as an alternative to manufacturing with metal, injection molding has proven itself as an affordable and efficient way to give cable assemblies the physical properties they need. Here’s a look at how the process works, its pros and cons, the components it can be used to build, and why it matters for your business
How Plastic Molding Works
The first step in plastic molding is creating a mold according to the design of the final product. This is commonly done by 3D printing, computer numerical control (CNC) machining, or electrical discharge machining (EDM), and is often the most expensive part of the otherwise cost-effective process. Once the mold has been formed, thermoplastic resins are injected into it by a large plunger or screw after being heated to a molten plastic phase. After the molten material has filled the cavity, it is allowed to cool until the final part is solidified and ready for tooling.
Types of Plastic Molding
There are several different types of plastic injection molding used by the experts in plastic injection molding like NAI. Each one offers unique advantages with the end product. They are:
- Vertical injection molding: Here the plastic is injected vertically into a mold attached underneath it, enabling the plastic to flow uniformly into the mold. Manual or robotic extraction is required, but parts can be made in greater detail, and uniform thickness is easier.
- Horizontal injection molding: Instead of injecting the fluid down into the mold, the molten plastic is pumped horizontally into an awaiting cavity. This process works especially well for parts with cylindrical geometry.
- Insert molding: Also known as single-shot overmolding, insert molding allows components like coaxial cables to be placed into the mold, and then surrounded by molten plastic until it cools for a protective finish.
- Liquid Silicone Molding (LSM): This thermoset process consists of two liquid polymer chemicals which are joined in a pressurized mixing chamber and fed to the injection unit on the molding machine. Once injected into the heated mold, the product cures into a flexible, water-tight product for either over-molded or insert molded applications with high chemical and temperature resistance.
- Overmolding: Sometimes performed in a double-shot process with multiple injection pumps, a series of layers can be added to core components, each with its material properties.
These molding process types are used in NAI manufacturing plants in Michigan, China, and U.S. By leveraging its expert experience in plastic molding and global talent, NAI is able to create the best in plastic molded products.
In addition to being high-yield, relatively inexpensive processes, these plastic molding methods also allow manufacturers to easily customize products. By adding simple additives or using different polymers, manufacturers may customize the color or finish of their product to match their brand — and may also modify physical properties, like electrical conductivity or corrosion resistance. Cable assemblies that must possess varying degrees of rigidity may also be built using durometers to customize hardness levels at each layer, creating flexibility where it’s needed the most.
Components Made Through Plastic Molding
The efficiency and versatility of the plastic molding process make it ideal for fabricating many components needed for electromechanical assemblies, cable assemblies, and harnesses. Here are some of the most common components where plastic injection molding comes into play.
Cable Assembly Components
Although the cables may have a ribbon or coaxial configuration, a cable assembly consists of multiple wires arranged into a single bundle and held together by the necessary connecting components. These include:
- Fasteners and grommets: Many types of fasteners are needed to bundle complex wire configurations, and grommets lock housing components together. Plastic molding can be used to make parts of many sizes, including high yields of fasteners that hold cables in place.
- Connectors, dongles, and adapters: These plug directly into computers and adapters connect different assemblies, but they are all molded in plastic.
Strain Reliefs: When sturdy interconnects must be built to withstand pulls and strains, plastic molding is the method of choice to create a strain relief that protects the cable from damage at the connection point. - Sheaths and shields: Sheaths are the outer layer that guards cable assemblies against the elements, and shields protect wires from electromagnetic/radio-frequency (EM/RF) interference. Insert molding and overmolding add protective layers to cables, protecting them from physical and electrical damage.
- Boots, bushings, ferrules, and more: Injection molding can provide for a variety of needed components for an assembly.
While jacketing may be used to sheathe core copper conductors or fiber optics, nearly every other component can be built using some form of plastic molding injection process. This photo shows several sample molded components used in cable assemblies.
Connector House Units
Also known as blocks, shells, or bodies, connector house units encapsulate cable assembly contacts. They’re not complete until their pins and screws are attached, but while the pins themselves are not made by plastic molding, the housings that hold them are.
Cable interconnects come in a wide variety of shapes and sizes, and they vary by their application. This makes them well-suited to fabrication by plastic molding, where connector houses with intricate geometries can easily be made. NAI’s cutting-edge machining facilities enable us to quickly build a mold with the desired geometry, customizing connector housings in the quantity that the client needs.
Cable Harness Assemblies
Comprised of cables that converge into a single contact, a cable harness assembly can be made by plastic molding in several ways. First, a protective sheath may coat the surface of individual cables, giving them the insulation and flexibility that each one needs. Screws and pins can then be added to the mold via insert molding to complete connection houses, and entire harness assemblies can be overmolded to give the desired finish.
Whether it’s the multiple colors needed for color-coding complex wiring diagrams or the one-shot process of inserting molding metal components into connector houses, plastic molding is the most efficient way to get the job done.
Applications of Plastic Molding
Cable assemblies can be found across a wide range of industries. If your application requires the use of electronic interconnects or an electromechanical assembly, plastic molding was probably involved. Some of the most common industry applications are:
- Medical cable assemblies
- Coax cable assemblies
- Cable harness assemblies
- Telecommunications interconnects
- Box build assemblies
- Robotics devices
- Industrial and medical-grade components
- Much more
For applications requiring specialized features, NAI is also able to perform custom molding on certain cable components. Contact a custom molding expert today for input on your application, and we’ll show you how we can help.
Connect with NAI, Experts in Plastic Molding
NAI is a leading custom cable assembly and harness manufacturer. We are one of the premier industrial, medical, and telecom cable assembly operations and can design a cable assembly (or assemblies) for a wide variety of applications. Contact NAI, experts in Plastic Molding today about your assembly application.